Prime PrepaintedHot-Dip and Galvanized Steel Coil CNBM
- Ref Price:
-

- Loading Port:
- Guangzhou
- Payment Terms:
- TT OR LC
- Min Order Qty:
- 20 m.t.
- Supply Capability:
- 3000 m.t./month
Add to My Favorites
Follow us:
OKorder Service Pledge
Quality Product, Order Online Tracking, Timely Delivery
OKorder Financial Service
Credit Rating, Credit Services, Credit Purchasing
Quick Details
Standard: | AISI, ASTM, GB, JIS | Grade: | Q195/235/345,ASTM A36,SS400,SPHC | Thickness: | 1.5-25mm |
Technique: | Hot Rolled | Application: | Container Plate | Special Use: | High-strength Steel Plate |
Width: | 300-1500mm | Length: | coil | Surface Treatment: | black/bright/galvanized,etc |
Authentication: | ISO9001-2008,SGS.BV,etc |
|
|
|
|
Packaging & Delivery
Packaging Details: | tandard seaworthy export package or as customers required |
Delivery Detail: | within 25 days after confirming the order |
Sepcification and Feature
Item | hot rolled pickled and oiled steel coil tianjin specialized manufacturing |
Brand Name | TJXH |
Business Type | A- level agency |
| Minerals & metallurgy |
Thickness | 1.8-20mm |
Width | 914-2000mm |
Coil weight | about 25 tons |
Material Grade | A36,Q195,Q235,SS400,SPHC,ST37/52 |
Technique | hot rolled |
Standard | AISI,ASTM,DIN,GB,JIS |
Test | With Hydraulic Testing, Eddy Current , Infrared Test |
Application | Construction,mechine,container manufacture, shipping building, bridge and other field |
Surface | 1) Bared 2) Black Painted (varnish coating) 3) Galvanized 4) Oiled 5) PE,3PE, FBE, corrosion resistant coating, Anti corrosion coating. chromated and oiled, chromated and non-oiled |
Package | in bundles, covered with waterproof-paper,strapped by strips. Or as customer’s requirement |
Sample | Common products, we can provide freely, for special production,we can depends on negotiation. |
MOQ | 20 tons |
Payment | 100% L/C at sight, 30% T/T in advance, and the balance against the copy of B/L or negotiation |
Delivery time | Within 10-25 days, according to quantity, asap save customer’s time |
Certificate | ISO |
What is the application of Steel Coil?
There are two sides,one is out side: Workshop, agricultural warehouse, residential precast unit, corrugated roof, roller shutter door, rainwater drainage pipe, retailer booth;the other is inside: Door, doorcase, light steel roof structure, folding screen, elevator, stairway, vent gutter.
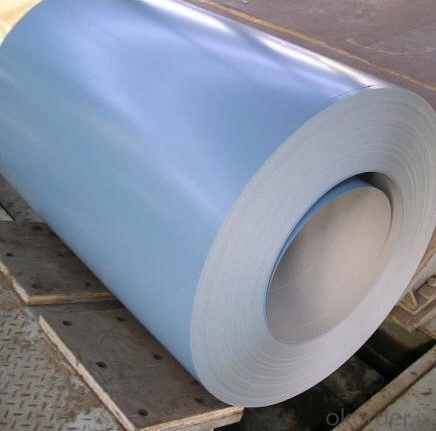
- Q: What are the different types of steel coil finishing equipment?
- There are several different types of steel coil finishing equipment used in various industries. These equipment are designed to perform specific tasks to ensure the steel coils are prepared and finished according to the desired specifications. Some of the commonly used types of steel coil finishing equipment include:
1. Slitting lines: Slitting lines are used to cut large steel coils into narrower strips. These machines have multiple slitting knives that can cut through the coil at high speeds, resulting in precise and clean cuts. Slitting lines are typically used in industries such as automotive, construction, and packaging.
2. Leveling lines: Leveling lines are used to flatten and straighten steel coils that may have uneven surfaces or irregularities. These machines use a combination of leveling rolls and tension control systems to ensure that the steel coils are perfectly flat and have consistent thickness throughout. Leveling lines are commonly used in the manufacturing of appliances, furniture, and metal roofing.
3. Recoiling lines: Recoiling lines are used to rewind steel coils into smaller coils of a specific diameter and weight. These machines are equipped with winding units that carefully wind the steel strip around a mandrel, creating compact and evenly wound coils. Recoiling lines are typically used in industries such as electrical, HVAC, and steel distribution.
4. Cut-to-length lines: Cut-to-length lines are used to cut steel coils into specific lengths as per the customer's requirements. These machines have precision measuring systems that accurately measure the length of the coil and hydraulic shears that cut the coil accordingly. Cut-to-length lines are commonly used in industries such as manufacturing, construction, and fabrication.
5. Coating lines: Coating lines are used to apply protective coatings or finishes on steel coils to enhance their corrosion resistance, durability, and appearance. These lines typically consist of cleaning and pre-treatment sections, where the coils are cleaned and treated with chemicals, followed by coating application sections where the desired coating material is applied. Coating lines are commonly used in industries such as automotive, appliances, and construction.
These are just a few examples of the different types of steel coil finishing equipment available in the market. Each type serves a specific purpose and plays a crucial role in the manufacturing and processing of steel coils for various applications.
- Q: How do steel coils contribute to the strength and durability of structures?
- Steel coils contribute to the strength and durability of structures by providing a high tensile strength and resistance to deformation. The coils are typically made from high-quality steel, which has excellent structural properties. When used in construction, steel coils can be shaped and formed into various structural components, such as beams, columns, and trusses. These components add strength and stability to the structure, making it more resistant to external forces, such as wind, earthquakes, and heavy loads. Additionally, steel coils are highly durable and can withstand harsh environmental conditions, including corrosion and extreme temperatures, ensuring the long-term integrity of the structure.
- Q: How are steel coils used in the production of metal fixtures?
- The production of metal fixtures relies heavily on steel coils, an indispensable element. Typically composed of carbon steel, these coils act as the primary raw material for manufacturing a diverse array of metal fixtures.
To begin the process, the steel coils are initially uncoiled and subsequently cut into sheets of the desired size and thickness. These sheets serve as the fundamental material for various types of metal fixtures, including brackets, hinges, handles, and other structural components.
Once the sheets have been cut, they undergo a series of shaping procedures, such as bending, stamping, or rolling. These procedures are crucial in molding the steel sheets into the specific design required for each metal fixture. For instance, bending can be utilized to create brackets or angles, while stamping can form intricate patterns or shapes.
Following the shaping procedures, it is common for the steel sheets to undergo welding or joining techniques, which are employed to assemble multiple components of the metal fixture. Through welding, the various parts are securely attached, ensuring strength and durability in the final product.
Moreover, steel coils also play a vital role in enhancing the appearance and extending the lifespan of metal fixtures. They can be coated or treated with protective layers, such as galvanized or powder coatings, to prevent corrosion and provide a polished finish. These coatings guarantee that the metal fixtures can withstand environmental factors and prolong their durability.
To summarize, steel coils are an indispensable component in the production process of metal fixtures. They are transformed into sheets, which are then shaped, joined, and coated to create a wide range of functional and aesthetically pleasing metal fixtures utilized across various industries.
- Q: What are the different types of steel coil finishing machines?
- There are several different types of steel coil finishing machines, each designed to perform specific tasks and achieve desired results. Some common types include:
1. Slitting Machines: These machines are used to slit large steel coils into narrower strips of desired widths. They consist of a set of circular blades that cut through the coil as it passes through the machine, creating multiple smaller coils or strips.
2. Cut-to-Length Machines: These machines are used to cut steel coils into specific lengths. They can be programmed to make precise cuts at predetermined lengths, ensuring accuracy and consistency.
3. Recoiling Machines: Recoiling machines are used to rewind steel coils into tight, compact rolls. They are typically used to create smaller coils from larger ones or to rewound coils that have become loose or damaged.
4. Edging Machines: Edging machines are used to remove excess material from the edges of steel coils, improving their overall appearance and ensuring consistent width throughout the coil.
5. Coating Machines: These machines are used to apply various coatings or finishes to the surface of steel coils, such as paint, galvanized coatings, or protective films. They often incorporate drying or curing systems to ensure proper adhesion and durability of the applied coatings.
6. Packaging Machines: Packaging machines are used to wrap or package steel coils for transportation or storage. They can wrap the coils in protective materials, such as plastic or paper, and secure them with strapping or other fastening methods.
7. Inspection Machines: These machines are used to inspect the quality and integrity of steel coils. They can detect defects, such as cracks, scratches, or surface irregularities, and provide feedback for quality control purposes.
These are just a few examples of the different types of steel coil finishing machines available. Each machine serves a specific purpose in the steel coil finishing process, ensuring that the final product meets the desired specifications and quality standards.
- Q: What are the cost implications of using steel coils in manufacturing?
- The cost implications of using steel coils in manufacturing can vary depending on several factors. Firstly, the price of steel coils themselves can fluctuate due to market conditions, supply and demand, and global trade policies. Additionally, the cost of transporting and storing steel coils can add to the overall expenses. Furthermore, the manufacturing process may require additional equipment or specialized machinery to handle and process steel coils, which can impact the overall production costs. However, steel coils are often considered a cost-effective option in manufacturing due to their durability, versatility, and recyclability, which can contribute to long-term savings and environmental benefits.
- Q: When steel is cast, does it become weaker/more brittle or anything of this nature? what are the side effects of steel casting on the steel itself?How can you correct these?
- It contains too many air bubble spacing and too many impurity that make it easily to be broken apart. Melt it down again with high heat to remove most impurity, after this process,it becomes iron.
- Q: How are steel coils protected during shipping?
- Steel coils are typically protected during shipping by being wrapped in a moisture-resistant material such as plastic or wax paper. They are also often secured with steel straps or bands to prevent shifting or damage during transit. Additionally, wooden or metal cradles are used to provide support and stability while in transport.
- Q: How are steel coils inspected for thickness using ultrasonic testing?
- Steel coils can be inspected for thickness using ultrasonic testing, which is a non-destructive testing method. In this process, a handheld ultrasonic thickness gauge is used to measure the thickness of the steel coil.
The ultrasonic thickness gauge emits high-frequency sound waves that travel through the steel coil. These sound waves bounce back from the backside of the coil, creating an echo. The time taken for the echo to return to the gauge is measured and used to calculate the thickness of the coil.
The gauge consists of a transducer that emits the sound waves and a receiver that detects the echoes. The transducer is placed on the surface of the coil, and a coupling gel or oil is used to ensure a good acoustic contact between the transducer and the steel surface.
The transducer emits a short burst of sound waves, which penetrates through the steel coil and reaches the backside. When the sound waves encounter any changes in the thickness of the coil, such as defects or variations, they get reflected back to the transducer. The receiver detects these echoes, and the time between the emission and reception of the sound waves is measured.
Using the known speed of sound in steel, the time taken for the sound waves to travel through the coil and back can be converted into a thickness measurement. This provides an accurate assessment of the thickness of the steel coil at various points.
Ultrasonic testing is a reliable and efficient method for inspecting the thickness of steel coils. It allows for quick measurements without damaging the material, making it suitable for quality control and ensuring compliance with manufacturing specifications.
- Q: How do steel coils perform in corrosive environments?
- Steel coils typically perform well in corrosive environments due to their inherent resistance to corrosion. This is primarily because steel is an alloy composed of iron and other elements, such as carbon, which provides it with a protective layer known as a passive film. This passive film acts as a barrier between the steel surface and the corrosive elements, preventing direct contact and thus minimizing the risk of corrosion.
In addition to the passive film, steel coils can also be coated with various protective coatings to enhance their resistance against corrosion. These coatings, such as zinc or epoxy, provide an additional layer of protection and further extend the lifespan of the steel coils when exposed to corrosive environments.
However, it is important to note that the performance of steel coils in corrosive environments can still be influenced by factors such as the specific corrosive agent, exposure duration, and the presence of other contaminants. In highly aggressive environments, such as those with high humidity, saltwater exposure, or acidic chemicals, the protective layers on steel coils may deteriorate over time, leading to potential corrosion.
To ensure optimal performance in corrosive environments, it is advisable to select steel coils with corrosion-resistant properties, such as stainless steel or galvanized steel. Regular maintenance and inspections are also crucial to identify any signs of corrosion early on and take appropriate measures to prevent further damage.
Overall, steel coils offer good resistance to corrosion in most environments, but the severity of the corrosive conditions can ultimately impact their performance.
- Q: How are steel coils used in the production of wind turbines?
- Steel coils are used in the production of wind turbines to manufacture the tower, nacelle, and other structural components. The coils are processed and shaped into various parts, ensuring the turbines have a sturdy and durable construction. Additionally, steel coils are employed in the manufacturing of the turbine blades, providing strength and reliability to withstand the forces of wind.