Preheating Continuous Feeding system
- Loading Port:
- China Main Port
- Payment Terms:
- TT OR LC
- Min Order Qty:
- -
- Supply Capability:
- -
OKorder Service Pledge
OKorder Financial Service
You Might Also Like
Preheating Continuous Feeding system
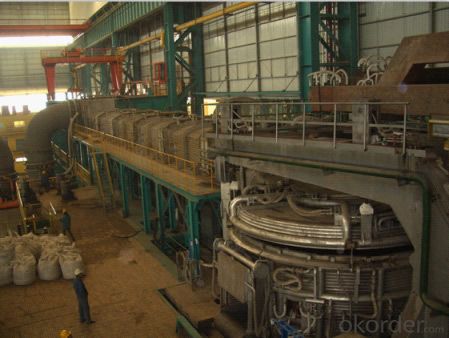
AE series preheating continuous feeding equipment is the most advanced, clean, energy saving and environmental protection metallurgy off gas using equipment in nowadays. This is using the off gas from the electric furnace to preheat the raw materials, and avoided the high failure rate, complicated operation, can not charging materials continuously and etc weakness from Shaft furnace preheating and preheating bucket and etc traditional ways. This system has been put into production in more than 20 factories in china and several other countries. And had gain marked affects in electricity saving, energy saving, production increasing, pollution reduction, and brings great economic benefits for customers.
AE series preheating continuous feeding equipment has characteristics of continuous feeding, continuous melting, continuous smelting and etc… which advantages are: short smelting period, low power consumption, low noises, low investment cost and etc…
Compared with the traditional EAF, the technical index of continuously preheating and feeding EAF process are:
1. Production capacity increases more than 10%.
2. Smelting cycle is shortened by 10-15 Min.
3. Save energy of 100-120kw.h/t for per ton Steel.
4. Electrode consumption decreases by 0.5-0.8%, Refractory material consumption reduces by 5%.
5. 20-30% reduction of CO2 volume which is released from per ton of Steel; Production site dustiness less than 10mg/M3.
6. Dioxin and CO emissions meets relative emission standards, smoke and dust is decreased from 17kg/t to 11kg/t.
7. Fully utilization of waste heat: On the Conveyor section can preheat the materials up to 300 degree Celsius and higher, and add burner in conveyor section, can raise the materials up to 600 degree Celsius. The rear part of the waste heat can be used to generate electricity or heating by steam which is produced by waste heat boiler, the gas from the boiler basically can go into the bag type dust collector directly. But the traditional electric furnace system off gas must go through the water cooled pipes, air forced cooler and etc equipments, it will consumable much energy to cool the temperature down and then can put the gas go into dust collector, so waste the energy from the off gas.
8. De-duster Fan power reduces 30%.
9. Noise is less than 90 decibels during the electric furnace smelting cycle.
With fully considering for customers kinds of actual using status, AE series preheating continuous feeding equipment brings direct economic benefits to customers by lowest failure rate, highest energy saving index, biggest investment return.
Main Technical Specifications
| Specification of | Dimensions of | Processing | Electric furnace |
(width*length) | (width*depth*length) | (t/h) | (t) | |
AE20S | 1260*65000 | 300*300*500 | 120 | 15-20 |
AE40S | 1400*46300 | 400*400*700 | 150 | 30-40 |
AE60S | 1840*48800 | 450*450*1000 | 200 | 50-60 |
AE70S | 2060*60000 | 500*500*1100 | 250 | 70 |
AE90S | 2140*60000 | 500*500*1100 | 300 | 80-90 |
AE150S | 2260*65000 | 500*500*1200 | 350 | 100-150 |
- Q: Selection of heat preservation material for industrial furnace
- Micro nano heat insulation board.The thermal conductivity of micro nano heat insulation board is very low, only a fraction of the traditional thermal insulation material, and the insulation effect is very efficient.
- Q: What is the difference between industrial furnaces and boilers?
- Industrial kilns and industrial furnaces are collectively referred to as industrial furnaces. Industrial furnaces mainly refer to devices that heat materials by combustion reactions.
- Q: Heat treatment equipment (industrial furnace), which products generally contain what kind of, which industries need to use heat treatment industrial furnace equipment.
- Heat treatment furnace is mainly for the mechanical processing and casting industry workpiece annealing, quenching, carburizing, quenching and tempering, heat treatment equipment.
- Q: What are the companies in the world that are currently engaged in metallurgical furnaces?
- There are many kinds of furnaces in metallurgical industry,colored and black,smelting and heat treatment are also included.
- Q: What is industrial furnace masonry?
- Masonry industrial furnaces refers to complete materials such as brick kilns in construction process.
- Q: What are the advantages of a vacuum furnace?
- The accuracy of furnace temperature measurement and monitoring is obviously improved. The indicating temperature of the thermocouple and the temperature of the furnace reach 1.5 C. But there is a large temperature difference in a large number of workpieces in different parts of the furnace. If the forced circulation of the rarefied gas is adopted, the temperature range of the temperature range of + 5 DEG C can still be controlled.
- Q: What is the difference between industrial furnace masonry and ordinary masonry?
- Industrial furnace masonry requirements are relatively high, industrial furnaces of different uses, whether material or masonry process, have strict requirements.
- Q: Brief introduction to repair of industrial furnace
- The industrial furnace is the main production equipment in the machinery industry. The repair of industrial furnace directly affects the quality, high yield, long life, low consumption and safe production of the furnace.
- Q: What is the difference in structure between industrial furnace and boiler?
- From the way: industrial furnace (electricity, natural gas, gas, induction heating is considered electricity), boilers (coal, all kinds of hot exhaust gas, a variety of gas, seemingly less electricity).
- Q: What is an industrial furnace pit?
- Later, a chamber kiln with a semi closed or fully enclosed kiln made of refractory bricks can be used as fuel for coal, gas or oil, and electricity can be used as heat source. The workpiece will be heated in the kiln hearth.
Send your message to us
Preheating Continuous Feeding system
- Loading Port:
- China Main Port
- Payment Terms:
- TT OR LC
- Min Order Qty:
- -
- Supply Capability:
- -
OKorder Service Pledge
OKorder Financial Service
Similar products
Hot products
Hot Searches