E Glass Or C Glass Twisting and Plying Yarns
- Loading Port:
- Shanghai
- Payment Terms:
- TT or LC
- Min Order Qty:
- 20000 kg
- Supply Capability:
- 200000 kg/month
OKorder Service Pledge
OKorder Financial Service
You Might Also Like
Description:
C-or E-textile glass a kind of additional twisting and plying yam. With the characteristics of high strength, corrosion resistance, heat resistance and high moisture absorption, no-alkali yam has high electric insulation, so it used to produce weaved wires and cables’ wrap cladding, protection sleeve, train of mine, insulation materials of electric machinery, every yam of woven cloth and other industrial yam. It can also supply big and little paper cube and other cube yams with different shapes and different roll weight.Product Features:
● Good Dispersibility.
● Less fuzzy.
● Density Even. Product Specifications:
Product Code | Tex | diameter (um) | Sizing. | breaking strength | Twist |
CC7.5-22-1/2 110S | 44 | 7.5 | paraffin | ≥15.5 | 110±10 |
EC9-33-1/2 65S | 66 | 9 | ≥24.1 | 65±5 | |
EC8-25-1/2 65S | 50 | 8 | ≥19.2 | 65±5 | |
CC9-33-1/2 65S | 33 | 9 | ≥20.6 | 65±5 | |
CC11-44-6/0 | 264 | 11 | ≥81.6 | ||
CC11-44-1/3 110S | 132 | 11 | silane | ≥40.8 | 28±3 |
EC9-68-1/0 28Z | 68 | 9 | ≥18.0 | 28±3 |
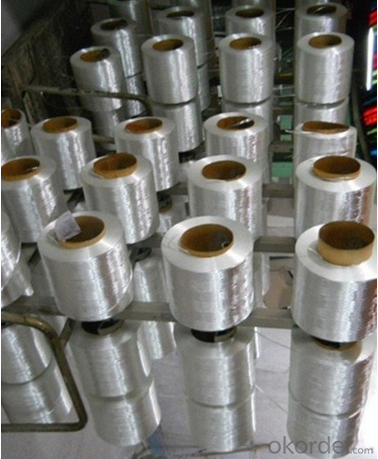
Packaging:
conforms to strict standards on packaging of every single cone to ensure customers' satisfaction, from inspection on appearance of cone, color difference, flaws, etc. before packaging to the selection of proper plastic bags, labels inside the cone, and carton packing.
- Q:Can fiberglass chopped strand be used in electrical grounding applications?
- No, fiberglass chopped strand should not be used in electrical grounding applications. Fiberglass is a non-conductive material, meaning it does not conduct electricity. In electrical grounding applications, a conductive material is required to ensure the safe dissipation of electrical charges. Copper or other metals are typically used for this purpose as they have good electrical conductivity.
- Q:Can glass fiber be recycle? There are raw silk and shred silk.. .
- Made into reinforced material
- Q:Can fiberglass chopped strand be used in the production of wind turbine hubs?
- Fiberglass chopped strand is indeed suitable for the production of wind turbine hubs. This type of glass fiber reinforcement is widely utilized across various sectors, including the manufacturing of wind turbine parts. It imparts strength, stiffness, and durability to the end product, making it a perfect material choice for wind turbine hubs. By combining the fiberglass chopped strand with resin and shaping it accordingly, a lightweight yet sturdy hub can be achieved, capable of withstanding the forces and stresses encountered during wind turbine operation. Moreover, fiberglass possesses corrosion resistance and outstanding fatigue resistance, rendering it highly suitable for long-term usage in wind turbine hubs.
- Q:Can fiberglass chopped strand be used in composite materials?
- Yes, fiberglass chopped strand can be used in composite materials. Fiberglass chopped strand consists of small, randomly chopped fibers made from glass. These fibers are typically mixed with a resin to create a composite material. The chopped strands provide reinforcement to the composite, enhancing its strength and durability. The use of fiberglass chopped strand in composites is common in various industries, including automotive, aerospace, construction, and marine. It is an effective and cost-efficient way to add strength and stiffness to composite materials, making them suitable for a wide range of applications.
- Q:Does fiberglass chopped strand improve the impact resistance of composite materials?
- Composite materials can benefit from the use of fiberglass chopped strand, as it effectively enhances their impact resistance. By incorporating small, randomly oriented fibers into the manufacturing process, the chopped strand reinforces the composite material. In the event of an impact, the fiberglass chopped strand plays a crucial role in distributing and absorbing the force, thereby preventing concentrated damage. Acting as a protective barrier, the fibers disperse the impact energy throughout the composite material, reducing the likelihood of cracks or fractures. Moreover, fiberglass chopped strand also improves the interfacial bonding between the fibers and the composite's matrix, resulting in better load transfer capabilities. This enhanced bonding strength significantly contributes to the overall impact resistance of the composite material. To summarize, the inclusion of fiberglass chopped strand in composite materials greatly enhances their impact resistance by effectively dispersing and absorbing impact energy, preventing localized damage, and improving the overall strength and durability of the composite.
- Q:What are the typical hardness properties of fiberglass chopped strand composites?
- The typical hardness properties of fiberglass chopped strand composites can vary depending on the specific composition and manufacturing process. However, fiberglass chopped strand composites generally exhibit good hardness properties, with a high resistance to scratching and indentation. This makes them suitable for various applications where hardness and durability are important, such as automotive parts, marine equipment, and construction materials.
- Q:How is the interlaminar shear strength of fiberglass chopped strand composites determined?
- Fiberglass chopped strand composites undergo assessment of their interlaminar shear strength using a standardized testing technique known as the short beam shear (SBS) test. This test has been specifically devised to gauge the shear strength existing between the layers of laminated composites. The SBS test necessitates the production of a small beam specimen from the fiberglass chopped strand composite material. Typically, this specimen takes on a rectangular shape with specified dimensions in terms of width, thickness, and length. The width and thickness are selected based on the particular requirements of the material under examination. During the test, the specimen is positioned on two supports, thereby creating a span. At the midpoint of this span, a load is applied, causing the specimen to bend. This bending action engenders shear stresses within the composite material. By measuring the load applied and the resulting deflection, the interlaminar shear strength can be determined by employing the principles of mechanics. The interlaminar shear strength is typically portrayed as the maximum shear stress the material can endure until failure occurs. This property holds great significance in evaluating the integrity and performance of fiberglass chopped strand composites, as it ascertains the material's resistance to delamination or separation between layers. The SBS test is extensively employed within the industry for the purpose of quality control, material selection, as well as research and development endeavors. It furnishes valuable information pertaining to the interlaminar shear strength of fiberglass chopped strand composites, aiding engineers and manufacturers in making well-informed decisions concerning the appropriateness of the material for specific applications.
- Q:Is fiberglass chopped strand suitable for wind turbine blades?
- Yes, fiberglass chopped strand is suitable for wind turbine blades. Fiberglass is a popular material choice for wind turbine blades due to its lightweight, high strength, and durability properties. Chopped strand fiberglass, which consists of small fibers randomly oriented and held together with a binder, can be easily molded and manufactured into complex shapes, making it ideal for wind turbine blade production. The fibers provide excellent stiffness and strength, enabling the blades to efficiently capture wind energy and withstand the stresses and forces experienced during operation. Additionally, fiberglass is corrosion-resistant, reducing maintenance and prolonging the lifespan of the blades. Overall, fiberglass chopped strand is a suitable and widely used material in the construction of wind turbine blades.
- Q:Can fiberglass chopped strand be used in aerospace exterior components?
- Aerospace exterior components can utilize fiberglass chopped strand. This specific type of fiberglass is known for its lightweight nature and strength, making it a popular choice in the aerospace industry. It possesses excellent mechanical properties, a high strength-to-weight ratio, and resistance to corrosion. Chopped strand refers to fiberglass that has been cut into shorter lengths, making it easier to handle and process. In the aerospace field, chopped strand is valuable for reinforcing composite materials used in exterior components like panels, fairings, and radomes. These components necessitate lightweight, durable materials with good impact resistance. By incorporating fiberglass chopped strand, the composite materials gain these desirable qualities, rendering it suitable for aerospace exterior components. Additionally, fiberglass chopped strand finds application in the production of aerospace components using techniques like resin transfer molding (RTM) or vacuum infusion. These processes enable the creation of intricate, lightweight parts that meet the exacting requirements of the aerospace industry. Nonetheless, it is crucial to acknowledge that utilizing fiberglass chopped strand in aerospace applications may necessitate additional certifications and testing to ensure compliance with safety standards and regulations.
- Q:What are the typical fiber lengths used in fiberglass chopped strand?
- Depending on the specific application and requirements, the typical lengths of fibers used in fiberglass chopped strand can vary. However, it is most common for the fibers to range from 3-6 mm (1/8-1/4 inch). These shorter fiber lengths are preferred because they disperse and distribute better within the resin matrix, resulting in improved overall strength and performance of the fiberglass composite. Additionally, shorter fibers help prevent entanglement and clumping during processing. It is worth noting that longer fiber lengths can also be used in specialized applications where increased strength or specific properties are desired. Ultimately, the choice of fiber length in fiberglass chopped strand depends on the specific needs and characteristics of the intended end use.
1. Manufacturer Overview |
|
---|---|
Location | |
Year Established | |
Annual Output Value | |
Main Markets | |
Company Certifications |
2. Manufacturer Certificates |
|
---|---|
a) Certification Name | |
Range | |
Reference | |
Validity Period |
3. Manufacturer Capability |
|
---|---|
a)Trade Capacity | |
Nearest Port | |
Export Percentage | |
No.of Employees in Trade Department | |
Language Spoken: | |
b)Factory Information | |
Factory Size: | |
No. of Production Lines | |
Contract Manufacturing | |
Product Price Range |
Send your message to us
E Glass Or C Glass Twisting and Plying Yarns
- Loading Port:
- Shanghai
- Payment Terms:
- TT or LC
- Min Order Qty:
- 20000 kg
- Supply Capability:
- 200000 kg/month
OKorder Service Pledge
OKorder Financial Service
Similar products
New products
Hot products
Hot Searches
Related keywords