All Categories
- - Steel Wire Rod
- - Steel Coils
- - Steel Profiles
- - Steel Pipes
- - Stainless Steel
- - Tinplate
- - Special Steel
- - Steel Sheets
- - Steel Rebars
- - Steel Strips
- - Hot Rolled Steel
- - Cold Rolled Steel
- - Pre-painted Steel
- - Seamless Steel Pipe
- - Welded Steel Pipe
- - Hollow Steel Tubes
- - Galvanized Pipe
- - Stainless Steel Coil
- - Stainless Steel Sheet
- - Stainless Steel Plate
- - Stainless Steel Strips
- - Electrolytic Tinplate Coil
- - Electrolytic Tinplate Sheet
- - Stainless Steel Rebars
- - Solar Panels
- - Solar Water Heater
- - Solar Related Products
- - Solar Inverter
- - Solar Cells
- - Solar Light
- - Solar Energy Systems
- - Solar Controllers
- - Solar Mounting System
- - Solar Pump
- - Solar Chargers
- - Fiberglass Chopped Strand
- - Fiberglass Mesh Cloth
- - Composite Pipes
- - FRP Pultrusion Profiles
- - Fiberglass Mat Tissue
- - Fiberglass Fabrics
- - Fiberglass Mesh
- - Composite Tank
- - Fiberglass Mesh tape
- - Polymer
- - FRP Roofing Panel
- - Fiberglass Roving
- - Monolithic Refractories
- - Ceramic Fiber Products
- - Refractory Bricks
- - Raw Materials For Refractory
- - Suspended Platform
- - Cranes
- - Concrete Machinery
- - Earthmoving Machinery
- - Building Hoist
- - Road Building Machinery
- - Plastic Pipe Fittings
- - Plastic Tubes
- - Plastic Sheets
- - Agricultural Plastic Products
- - Plastic Nets
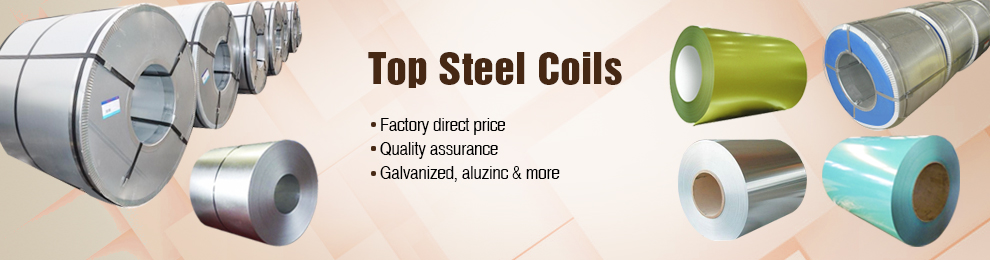
Q & A
How does the surface finish of electrolytic tinplate coil affect its resistance to scratching?
The surface finish of electrolytic tinplate coil greatly affects its resistance to scratching. A smooth and well-finished surface reduces the chances of scratches occurring, as it provides a protective layer against external forces. On the other hand, a rough or uneven surface finish is more prone to scratching, as it offers less resistance to abrasion. Therefore, a high-quality surface finish is crucial for enhancing the resistance to scratching in electrolytic tinplate coil.
What are the common tests performed on electrolytic tinplate coil?
The common tests performed on electrolytic tinplate coil include corrosion resistance testing, tin adhesion testing, coating weight measurement, roughness measurement, and visual inspection for any defects or imperfections.
Can electrolytic tinplate coil be used for packaging of meat and poultry?
Yes, electrolytic tinplate coil can be used for packaging of meat and poultry. Tinplate is a popular choice for food packaging due to its excellent corrosion resistance and ability to maintain product freshness. The electrolytic process ensures a smooth and uniform coating, making it suitable for direct contact with food products such as meat and poultry.
What are the common methods for surface finishing of electrolytic tinplate coil?
Common methods for surface finishing of electrolytic tinplate coil include:
1. Electroplating: This involves depositing a layer of tin onto the surface of the tinplate coil through an electrolytic process. It provides a smooth and shiny finish, enhancing the appearance and corrosion resistance of the coil.
2. Organic coating: This method involves applying a layer of organic material, such as lacquer or enamel, onto the tinplate coil's surface. It offers additional protection against corrosion and can also provide decorative finishes.
3. Chromium coating: A thin layer of chromium can be applied to the tinplate coil's surface through electroplating. This enhances the coil's resistance to corrosion and provides a bright, reflective finish.
4. Passivation: Passivation treatment involves applying a chemical solution to the tinplate coil's surface to remove any impurities and create a protective oxide layer. This improves the corrosion resistance of the coil.
These methods are commonly used in the industry to improve the appearance, durability, and corrosion resistance of electrolytic tinplate coil products.
Wholesale Electrolytic Tinplate Coil from supplier in Afghanistan
We are a Electrolytic Tinplate Coil supplier serving the Afghanistan, mainly engaged in the sale, quotation, and technical support services of various Electrolytic Tinplate Coil products in the Afghanistan region. We are a subsidiary platform of the Fortune Global 500 company CNBM, able to provide you with one-stop Electrolytic Tinplate Coil procurement services in the Afghanistan. Not only do we have a wide range of Electrolytic Tinplate Coil products, but after years of market development in the Afghanistan, we can also provide valuable experience for your projects.