All Categories
- - Steel Wire Rod
- - Steel Coils
- - Steel Profiles
- - Steel Pipes
- - Stainless Steel
- - Tinplate
- - Special Steel
- - Steel Sheets
- - Steel Rebars
- - Steel Strips
- - Hot Rolled Steel
- - Cold Rolled Steel
- - Pre-painted Steel
- - Seamless Steel Pipe
- - Welded Steel Pipe
- - Hollow Steel Tubes
- - Galvanized Pipe
- - Stainless Steel Coil
- - Stainless Steel Sheet
- - Stainless Steel Plate
- - Stainless Steel Strips
- - Electrolytic Tinplate Coil
- - Electrolytic Tinplate Sheet
- - Stainless Steel Rebars
- - Solar Panels
- - Solar Water Heater
- - Solar Related Products
- - Solar Inverter
- - Solar Cells
- - Solar Light
- - Solar Energy Systems
- - Solar Controllers
- - Solar Mounting System
- - Solar Pump
- - Solar Chargers
- - Fiberglass Chopped Strand
- - Fiberglass Mesh Cloth
- - Composite Pipes
- - FRP Pultrusion Profiles
- - Fiberglass Mat Tissue
- - Fiberglass Fabrics
- - Fiberglass Mesh
- - Composite Tank
- - Fiberglass Mesh tape
- - Polymer
- - FRP Roofing Panel
- - Fiberglass Roving
- - Monolithic Refractories
- - Ceramic Fiber Products
- - Refractory Bricks
- - Raw Materials For Refractory
- - Suspended Platform
- - Cranes
- - Concrete Machinery
- - Earthmoving Machinery
- - Building Hoist
- - Road Building Machinery
- - Plastic Pipe Fittings
- - Plastic Tubes
- - Plastic Sheets
- - Agricultural Plastic Products
- - Plastic Nets
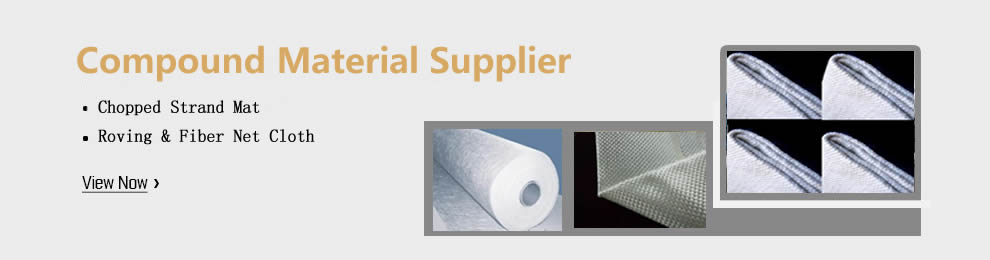
Q & A
What advancements in nanomaterials are contributing to the durability and strength of composite tanks?
Advancements in nanomaterials such as carbon nanotubes and graphene are contributing significantly to the durability and strength of composite tanks. These nanomaterials possess exceptional mechanical properties, including high tensile strength and stiffness, which enhance the overall structural integrity of composite tanks. Additionally, their unique properties like low weight, corrosion resistance, and thermal stability further improve the tanks' durability and longevity. By incorporating nanomaterials into the composite matrix, engineers can design tanks that are lighter, stronger, and more resistant to wear and tear, ultimately improving their performance and lifespan.
Can composite tanks be used in the nuclear industry for waste storage?
Yes, composite tanks can be used in the nuclear industry for waste storage. Composite materials such as fiberglass-reinforced plastic (FRP) offer excellent corrosion resistance, high strength-to-weight ratio, and durability, making them suitable for safely storing nuclear waste. These tanks can effectively contain and isolate hazardous materials, providing an efficient and cost-effective solution for waste storage in the nuclear industry.
What is a composite tank?
A composite tank is a type of storage tank that is made from a combination of materials, typically including a reinforced plastic or fiberglass shell with additional layers of various materials such as carbon fiber or Kevlar. These tanks are known for their strength, durability, and resistance to corrosion, making them ideal for storing a wide range of substances, including chemicals, fuels, and even water.
What is the difference between filament-wound and hand-laid composite tanks?
The main difference between filament-wound and hand-laid composite tanks lies in the manufacturing process and resulting properties. Filament-wound tanks are produced by winding continuous fibers, such as carbon or fiberglass, around a mandrel in a precise pattern. This automated process allows for consistent fiber placement and precise control over the orientation and thickness of the fibers, resulting in higher strength-to-weight ratios and better resistance to pressure and impact.
On the other hand, hand-laid composite tanks are built by manually layering the fibers in a predetermined pattern. While this process allows for greater flexibility and customization, it often leads to variations in fiber orientation and thickness, affecting the overall strength and performance of the tank. Hand-laid tanks are typically less efficient in terms of weight and may have slightly lower mechanical properties compared to filament-wound tanks.
In summary, filament-wound tanks offer superior mechanical properties, higher strength-to-weight ratios, and better quality control due to the automated manufacturing process. Hand-laid tanks, on the other hand, provide more flexibility in design but may sacrifice some performance and consistency.
Wholesale Composite Tank from supplier in Honduras
We are a Composite Tank supplier serving the Honduras, mainly engaged in the sale, quotation, and technical support services of various Composite Tank products in the Honduras region. We are a subsidiary platform of the Fortune Global 500 company CNBM, able to provide you with one-stop Composite Tank procurement services in the Honduras. Not only do we have a wide range of Composite Tank products, but after years of market development in the Honduras, we can also provide valuable experience for your projects.
Hot Search
- Fiberglass Chopped Strand in Eritrea
- Fiberglass Mesh Cloth in Somalia
- Composite Pipes in Cameroon
- FRP Pultrusion Profiles in Bhutan
- Fiberglass Mat Tissue in Denmark
- Fiberglass Fabrics in Kiribati
- Fiberglass Mesh in Estonia
- Composite Tank in Maldives
- Fiberglass Mesh tape in Indonesia
- Polymer in Nauru