Specifications
ductile iron pipe:
1. DN80-DN1600mm (T-Type, Class K9)
2.effective length 6m/pc
3.comply with ISO2531/EN545/EN598
Company Profile
CNBM International Corporation is the leading production base and renowned supplier of Ductile Iron Water Pipe systems of both potable and waste water in China. We are constantly looking to develop high quality products to ensure the longest service life and wonderful performance.
CNBM Pipelines regard quality as the essential factor leading to successful business. Every ductile iron pipe is tested in accordance with BS EN545 (water application) or BS EN598 (sewer application). CNBM Pipelines products comply with and are tested according to the relevant European and International Standards. Our pipes are manufactured under the quality management system BS EN ISO 9001. After years of efforts, CNBM Pipelines has built up great reputation in terms of quality and service among customers worldwide.
Product Introduction
CNBM ductile iron pipe ranges from DN80-DN1600mm (Tyton, T-Type, Class K7/K8/K9), effective length: 6m, complying with ISO2531and EN545 standards.
Specification& Payment terms
Internal lining: ductile iron pipes shall have an internal cement mortar lining in acc with ISO4179.
External coating: ductile iron pipes shall be externally coated with metallic zinc spray plus a further layer of resin painting to ISO8179.
Gasket: 100% SBR/NBR/EPDM rubber gasket in accordance with ISO4633.
Packing: ductile iron pipes from DN100 to DN300 be bundled with steel belts, others are in bulk.
Payment term: L/C, T/T.
Packing: In bulk vessel or in container
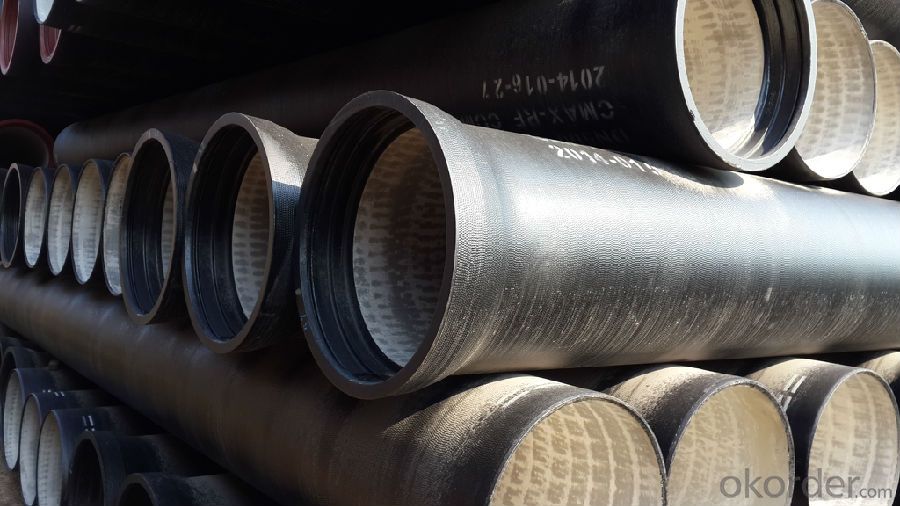
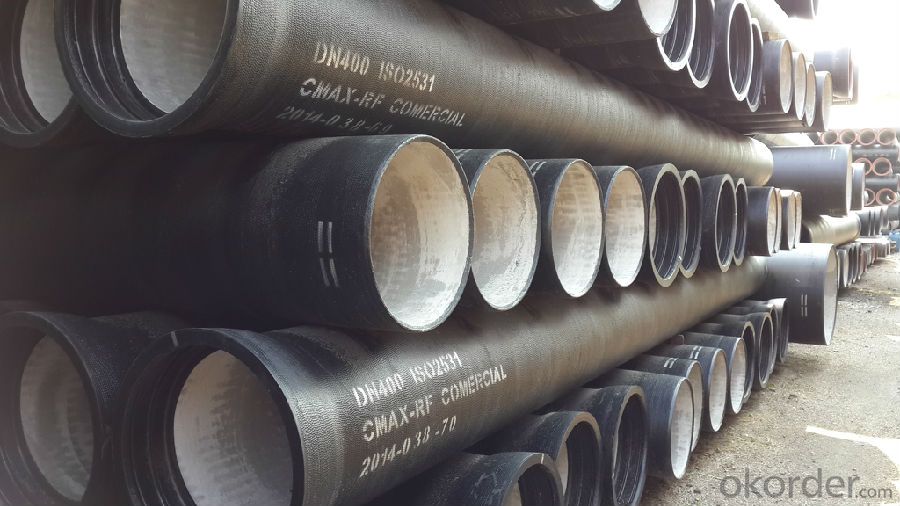