Alumina ceramic foam filter for molten aluminium
- Loading Port:
- China Main Port
- Payment Terms:
- TT OR LC
- Min Order Qty:
- -
- Supply Capability:
- -
OKorder Service Pledge
Quality Product, Order Online Tracking, Timely Delivery
OKorder Financial Service
Credit Rating, Credit Services, Credit Purchasing
You Might Also Like
APPLICATION:For the filtration of molten aluminum and non ferrous alloy.
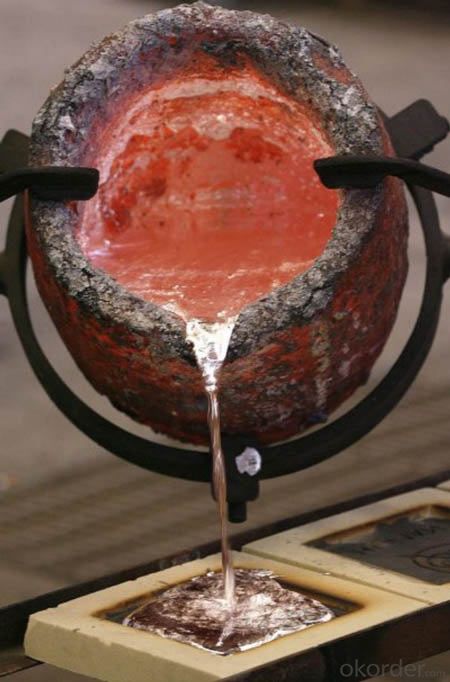
Alumina Ceramic Foam Filters mainly for filtration of aluminum and alloys in foundries and cast houses .With the excellent
resistance to attack and corrosion from molten aluminum, the filter can effectively remove inclusions, reduce trapped gas
and provide laminar flow and then the filtered metal is significantly cleaner.Cleaner metal results in higher-quality castings,
less scrap, and fewer inclusion defects, all of which contribute to bottom-line profit.
resistance to attack and corrosion from molten aluminum, the filter can effectively remove inclusions, reduce trapped gas
and provide laminar flow and then the filtered metal is significantly cleaner.Cleaner metal results in higher-quality castings,
less scrap, and fewer inclusion defects, all of which contribute to bottom-line profit.
-Reduce scrap related to inclusions.
-Reduce costs related to inclusion defects.
-Increase productivity with higher extrusion or rolling speeds.
-Increase casting flexibility with easy alloy changes.
-No holding metal.
FEATURES:
*Superior dimensional tolerances
*Stable chemical composition
*Highest filtration efficiency
*Excellent strength
*Resistant to corrosion attack by molten aluminum and alloys
*Beveled edges and compressible gasket
SPECIFICATION:
Color:White
Working Temp :≤1100°C
Porosity:80~90%
PPI(pores per inch):10/20/30/40
PPI(pores per inch):10/20/30/40
Compression Strength (Room Temperature) :≥0.8Mpa
Volume Density: 0.36-0.5g/cm3
Thermal Shock Resistance:1100°C to room temperature 6 times
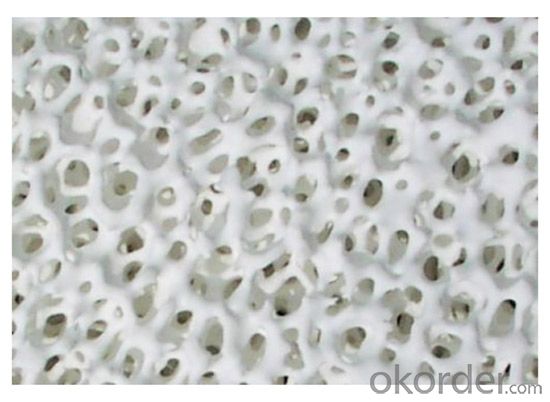
COMMON SIZES:
7x7x2" (178x178x50mm)
9x9x2" (229x229x50mm)
12x12x2" (305x305x50mm)
15x15x2" (381x381x50mm)
17x17x2" (432x432x50mm)
20x20x2" (508x508x50mm)
23x23x2" (584x584x50mm)
7x7x2" (178x178x50mm)
9x9x2" (229x229x50mm)
12x12x2" (305x305x50mm)
15x15x2" (381x381x50mm)
17x17x2" (432x432x50mm)
20x20x2" (508x508x50mm)
23x23x2" (584x584x50mm)
*Other sizes can be customized upon request.
- Q:What filter material are placed in the aquarium filter?
- Generally let off the filter cotton and ceramic rings, there are biochemical balls, coral bone, stone, activated carbon and so onConditional: filter cotton, ceramic ring, biochemical ball, coral bone, stone, activated carbon
- Q:Ceramic filter capacity.
- You ask too general, to say processing capacity (ie capacity), at least to provide material conditions, such as: material name, concentration, particle size distribution. In addition, the basic conditions of equipment operation should be taken into account.
- Q:How can I avoid the backwash pressure in the production of ceramic filter?
- Recoil of the ceramic filter is on the clean water under certain pressure, from the inside out flushing blockage blockage in the ceramic filter plate on the internal pore water pressure, the recoil is generally less than 0.12MPa, the pressure is too small or no recoil recoil effect is not good.
- Q:What about the leakage of the ceramic filter static and dynamic sealing points?
- The filtrate pump works to drain or recycle the water that has been pumped out. 6 、 cleaning system work, cleaning system includes backwashing (water pump pressure or height difference pressure), acid liquid (metering pump, automatic acid injection), ultrasonic (ultrasonic work), etc.. 7 、 control system and other electrical systems. In addition, the filter cake which is absorbed and dried on the ceramic filter plate is unloaded automatically by the scraper and then falls on the belt conveyor, and is conveyed to the concentrate storage yard by a belt conveyor. Other questions about ceramic filter, welcome to chat with me or look at my head
- Q:The ultrasonic wave of ceramic filter is not good. What's going on?
- The earliest filtration was mostly gravity filtration, which was followed by pressure filtration to increase the rate of filtration, followed by vacuum filtration. The drum vacuum filter invented in the early twentieth Century realized the continuous operation of the filter. Since then, various types of continuous filters have appeared. Intermittent operating filters (such as plate and frame press filters) are developed for automatic operation, and the filtration area is becoming larger and larger. In order to obtain the filter residue with low moisture content, the mechanical press filter has been developed.
- Q:What happens when the pressure on the filter plate is uneven during backwashing?
- Ceramic filter is a kind of solid-liquid separation, dehydration drying equipment, such as dehydration pulp, mortar. The backwash of ceramic filter is to flush the filter medium (ceramic filter plate) with clean water with a certain pressure.
- Q:The vacuum degree of the ceramic filter is normal and the cake water is large?
- There is a difference between the vacuum display and the actual vacuumThe main speed of the ceramic filter is too fastThe water content of the filter cake is gradually increased within 0~8 hours after the equipment has been continuously turned onThe ceramic filter plate does not meet the aperture range and the opening rate is lowThe ceramic filter plate has a near life and serious blockageCeramic filter cleaning standards (acid, ultrasonic, backwash water)The scraper can not be completely discharged, and the surface of the ceramic plate is coated with a thin filter cakeFailure to manufacture equipment or other causes of failure
- Q:The working principle of ceramic filter
- Based on the work principle of ceramic filter function of the capillary, by using porous ceramic as filter media, a large number of small capillary action with solid-liquid separation equipment design principle using microporous ceramic disc filter in negative pressure, working conditions, characteristics of the microporous ceramic filter plate with its unique water impermeable, extraction of ceramic filter plate and external vacuum cavity the differential pressure tank suspension material under the action of negative pressure adsorption in the ceramic filter plate, solid material can not through the microporous ceramic filter plate is retained on the surface of the ceramic plate, and the liquid due to the hydrophilic effect of vacuum pressure difference and the ceramic filter plate is passed into the gas-liquid distribution device (vacuum barrel) efflux or recycling so as to achieve the purpose of solid-liquid separation.
- Q:What are the materials that make up the ceramic mold?
- From the development trend of rice, the development of ceramic membrane preparation technology mainly in the following 2 aspects: one is the porous membrane research, to further improve the already commercialized inorganic ultrafiltration and microfiltration membrane, nanofiltration membrane with molecular sieve, the development function of gas separation membrane and pervaporation membrane: two in dense membrane research solid electrolyte membrane, ultra-thin metal and its alloy film and ion conduction ability is research hotspot. The commercial porous membranes are mainly ultrafiltration and microfiltration membranes, and their preparation methods are mainly particle sintering and sol-gel. The former is mainly used for making microporous filter membranes, and commercial A1203 films are prepared by particle sintering method.
- Q:Influence factors of ceramic filter
- On the other hand, as the spindle speed slows down, the thickness of the slurry is thickened, and the moisture of the concentrate is also affected. For viscous material, ceramic filter with ceramic plate to work as filter media, when the cake is formed gradually into the porous filter medium filter cake itself, and the cake is not easy to form a viscous material, forming a dry cake appearance does not slow, the spindle speed is easy to reduce the water content of concentrate. Similarly, the spindle speed is accelerated, the cake formation time in the vacuum zone is shortened, and the slurry thickness is reduced, and the material can be improved for the easy molding material. But the spindle speed is too fast to be cleaned after each cycle of the ceramic plate. As for the viscous material, the cake is difficult to form after the spindle speed increases, and it will affect the capacity. Therefore, the use of ceramic filter should focus on the inherent nature of the concentrate to explore the best spindle speed. Generally, the higher the temperature, the smaller the viscosity of the liquid, the more conducive to improve the filtration rate, reduce the cake or sediment water, while reducing the viscosity of the slurry, can improve the processing capacity.
1. Manufacturer Overview |
|
---|---|
Location | |
Year Established | |
Annual Output Value | |
Main Markets | |
Company Certifications |
2. Manufacturer Certificates |
|
---|---|
a) Certification Name | |
Range | |
Reference | |
Validity Period |
3. Manufacturer Capability |
|
---|---|
a)Trade Capacity | |
Nearest Port | |
Export Percentage | |
No.of Employees in Trade Department | |
Language Spoken: | |
b)Factory Information | |
Factory Size: | |
No. of Production Lines | |
Contract Manufacturing | |
Product Price Range |
Send your message to us
Alumina ceramic foam filter for molten aluminium
- Loading Port:
- China Main Port
- Payment Terms:
- TT OR LC
- Min Order Qty:
- -
- Supply Capability:
- -
OKorder Service Pledge
Quality Product, Order Online Tracking, Timely Delivery
OKorder Financial Service
Credit Rating, Credit Services, Credit Purchasing
Similar products
New products
Hot products
Related keywords