All Categories
- - Steel Wire Rod
- - Steel Coils
- - Steel Profiles
- - Steel Pipes
- - Stainless Steel
- - Tinplate
- - Special Steel
- - Steel Sheets
- - Steel Rebars
- - Steel Strips
- - Hot Rolled Steel
- - Cold Rolled Steel
- - Pre-painted Steel
- - Seamless Steel Pipe
- - Welded Steel Pipe
- - Hollow Steel Tubes
- - Galvanized Pipe
- - Stainless Steel Coil
- - Stainless Steel Sheet
- - Stainless Steel Plate
- - Stainless Steel Strips
- - Electrolytic Tinplate Coil
- - Electrolytic Tinplate Sheet
- - Stainless Steel Rebars
- - Solar Panels
- - Solar Water Heater
- - Solar Related Products
- - Solar Inverter
- - Solar Cells
- - Solar Light
- - Solar Energy Systems
- - Solar Controllers
- - Solar Mounting System
- - Solar Pump
- - Solar Chargers
- - Fiberglass Chopped Strand
- - Fiberglass Mesh Cloth
- - Composite Pipes
- - FRP Pultrusion Profiles
- - Fiberglass Mat Tissue
- - Fiberglass Fabrics
- - Fiberglass Mesh
- - Composite Tank
- - Fiberglass Mesh tape
- - Polymer
- - FRP Roofing Panel
- - Fiberglass Roving
- - Monolithic Refractories
- - Ceramic Fiber Products
- - Refractory Bricks
- - Raw Materials For Refractory
- - Suspended Platform
- - Cranes
- - Concrete Machinery
- - Earthmoving Machinery
- - Building Hoist
- - Road Building Machinery
- - Plastic Pipe Fittings
- - Plastic Tubes
- - Plastic Sheets
- - Agricultural Plastic Products
- - Plastic Nets
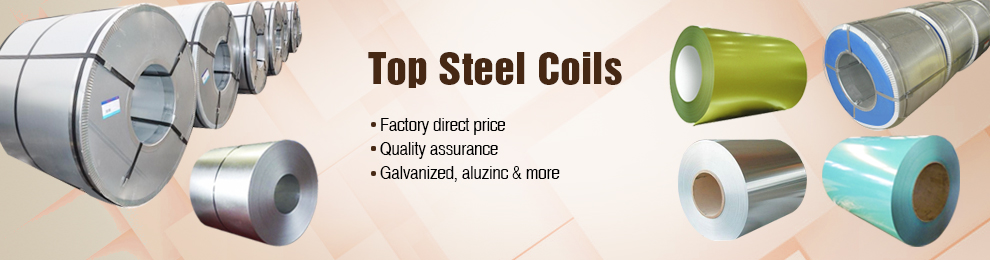
Q & A
How is a welded steel pipe tested for quality and durability?
A welded steel pipe is tested for quality and durability through various methods such as visual inspection, non-destructive testing techniques like ultrasonic testing, radiographic testing, and magnetic particle inspection. These tests ensure that the welds are free from defects, such as cracks or inclusions, and meet the required specifications. Additionally, the pipe may undergo hydrostatic testing, where it is pressurized to check for leaks or weaknesses. These rigorous testing procedures help ensure that the welded steel pipe meets the necessary quality and durability standards.
What is the difference between fusion welding and friction welding for welded steel pipe?
Fusion welding involves melting the edges of two steel pipes and then joining them together, typically using a filler material. This process requires a heat source, such as a flame or electric arc, to create the molten state needed for the welding. On the other hand, friction welding uses mechanical friction to generate heat at the joint interface, causing the surfaces of the steel pipes to melt and fuse together. This method does not require a separate heat source or filler material, as the frictional heat is enough to create a strong bond between the pipes. Overall, the main difference lies in the heat source used and the absence of filler material in friction welding, making it a more efficient and cost-effective process for welded steel pipe manufacturing.
Can welded steel pipes be used for oil and gas pipelines?
Yes, welded steel pipes can be used for oil and gas pipelines. Welded steel pipes are commonly used in the construction of oil and gas pipelines due to their durability, strength, and ability to withstand high pressure and extreme temperatures. The welded joints in these pipes provide a strong and reliable connection, ensuring the safe transportation of oil and gas over long distances.
What are the factors to consider when selecting the appropriate wall thickness for a welded steel pipe?
When selecting the appropriate wall thickness for a welded steel pipe, several factors need to be considered. These factors include the pipe's intended use, the pressure it will need to handle, the material being transported through it, the environmental conditions it will be subjected to, and any applicable industry standards or regulations. By taking these factors into account, the appropriate wall thickness can be determined to ensure the pipe's durability, structural integrity, and efficient operation.
What is the impact of tensile strength on the structural integrity of welded steel pipe?
Tensile strength plays a crucial role in determining the structural integrity of welded steel pipes. It refers to the maximum amount of tensile stress a material can withstand before breaking or undergoing deformation. In the case of welded steel pipes, a higher tensile strength is desirable as it ensures the pipe can withstand the internal and external forces it may encounter during operation. A lower tensile strength could result in the pipe experiencing permanent deformation or even failure, compromising the overall structural integrity. Therefore, a high tensile strength is vital for ensuring the strength and durability of welded steel pipes.
Wholesale Welded Steel Pipe from supplier in Eritrea
We are a Welded Steel Pipe supplier serving the Eritrea, mainly engaged in the sale, quotation, and technical support services of various Welded Steel Pipe products in the Eritrea region. We are a subsidiary platform of the Fortune Global 500 company CNBM, able to provide you with one-stop Welded Steel Pipe procurement services in the Eritrea. Not only do we have a wide range of Welded Steel Pipe products, but after years of market development in the Eritrea, we can also provide valuable experience for your projects.