All Categories
- - Steel Wire Rod
- - Steel Coils
- - Steel Profiles
- - Steel Pipes
- - Stainless Steel
- - Tinplate
- - Special Steel
- - Steel Sheets
- - Steel Rebars
- - Steel Strips
- - Hot Rolled Steel
- - Cold Rolled Steel
- - Pre-painted Steel
- - Seamless Steel Pipe
- - Welded Steel Pipe
- - Hollow Steel Tubes
- - Galvanized Pipe
- - Stainless Steel Coil
- - Stainless Steel Sheet
- - Stainless Steel Plate
- - Stainless Steel Strips
- - Electrolytic Tinplate Coil
- - Electrolytic Tinplate Sheet
- - Stainless Steel Rebars
- - Solar Panels
- - Solar Water Heater
- - Solar Related Products
- - Solar Inverter
- - Solar Cells
- - Solar Light
- - Solar Energy Systems
- - Solar Controllers
- - Solar Mounting System
- - Solar Pump
- - Solar Chargers
- - Fiberglass Chopped Strand
- - Fiberglass Mesh Cloth
- - Composite Pipes
- - FRP Pultrusion Profiles
- - Fiberglass Mat Tissue
- - Fiberglass Fabrics
- - Fiberglass Mesh
- - Composite Tank
- - Fiberglass Mesh tape
- - Polymer
- - FRP Roofing Panel
- - Fiberglass Roving
- - Monolithic Refractories
- - Ceramic Fiber Products
- - Refractory Bricks
- - Raw Materials For Refractory
- - Suspended Platform
- - Cranes
- - Concrete Machinery
- - Earthmoving Machinery
- - Building Hoist
- - Road Building Machinery
- - Plastic Pipe Fittings
- - Plastic Tubes
- - Plastic Sheets
- - Agricultural Plastic Products
- - Plastic Nets
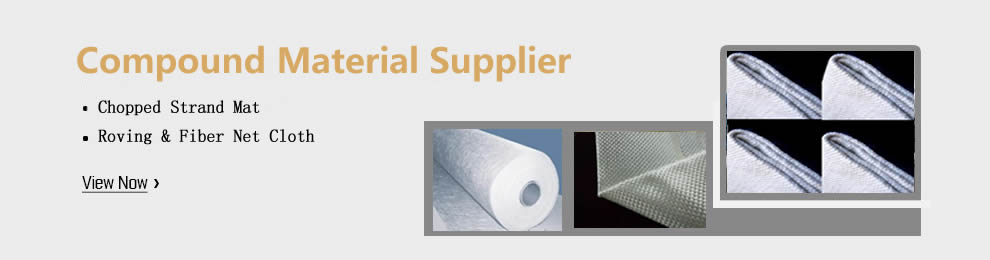
Q & A
How do composite tanks address concerns about chemical compatibility and reactivity?
Composite tanks address concerns about chemical compatibility and reactivity by utilizing materials that are specifically chosen to be resistant to the chemicals and reactants they will come into contact with. These tanks are designed to be non-reactive and non-permeable, ensuring that they can safely store and transport a wide range of substances without any risk of contamination or chemical reactions. Additionally, composite tanks undergo rigorous testing to ensure their chemical compatibility, providing a reliable solution for storing hazardous or corrosive materials.
What is the role of composite tank maintenance in prolonging their lifespan?
The role of composite tank maintenance in prolonging their lifespan is crucial. Regular maintenance helps identify and address any potential issues or damages early on, preventing further deterioration or failure. Proper cleaning and inspection of the tank's surface and structure help maintain its integrity, preventing corrosion or material degradation. Additionally, maintenance activities such as reapplying protective coatings or repairing minor damages ensure the tank's continued functionality and prevent major repairs or replacements, ultimately extending its overall lifespan.
How are composite tanks tested for strength and durability?
Composite tanks are tested for strength and durability through a series of rigorous assessments. These evaluations typically include non-destructive testing techniques such as ultrasonic and X-ray inspection to identify any defects or anomalies within the tank's structure. Additionally, the tanks undergo hydrostatic pressure testing, where they are subjected to internal pressure to ensure they can withstand the required levels without any signs of leakage or failure. Furthermore, composite tanks are often subjected to environmental tests, including exposure to extreme temperatures, humidity, and vibration to assess their ability to withstand various operating conditions. These comprehensive tests ensure that composite tanks meet the necessary strength and durability standards before they are deployed for use.
What is the process of manufacturing composite tanks?
The process of manufacturing composite tanks involves several steps. First, a mold is created based on the desired shape and size of the tank. Then, layers of composite materials, such as fiberglass or carbon fiber, are laid into the mold. These materials are typically pre-impregnated with resin to ensure proper adhesion and strength. The layers are carefully positioned and compacted to remove any air or voids. Next, the mold is placed into a curing oven where heat and pressure are applied to harden the resin and bond the layers together. Once cured, the tank is removed from the mold and undergoes finishing processes, such as trimming and polishing, to achieve the final desired shape and appearance. Finally, quality control checks are performed to ensure the tank meets all specifications and standards before it is ready for use.
Wholesale Composite Tank from supplier in Eritrea
We are a Composite Tank supplier serving the Eritrea, mainly engaged in the sale, quotation, and technical support services of various Composite Tank products in the Eritrea region. We are a subsidiary platform of the Fortune Global 500 company CNBM, able to provide you with one-stop Composite Tank procurement services in the Eritrea. Not only do we have a wide range of Composite Tank products, but after years of market development in the Eritrea, we can also provide valuable experience for your projects.