All Categories
- - Steel Wire Rod
- - Steel Coils
- - Steel Profiles
- - Steel Pipes
- - Stainless Steel
- - Tinplate
- - Special Steel
- - Steel Sheets
- - Steel Rebars
- - Steel Strips
- - Hot Rolled Steel
- - Cold Rolled Steel
- - Pre-painted Steel
- - Seamless Steel Pipe
- - Welded Steel Pipe
- - Hollow Steel Tubes
- - Galvanized Pipe
- - Stainless Steel Coil
- - Stainless Steel Sheet
- - Stainless Steel Plate
- - Stainless Steel Strips
- - Electrolytic Tinplate Coil
- - Electrolytic Tinplate Sheet
- - Stainless Steel Rebars
- - Solar Panels
- - Solar Water Heater
- - Solar Related Products
- - Solar Inverter
- - Solar Cells
- - Solar Light
- - Solar Energy Systems
- - Solar Controllers
- - Solar Mounting System
- - Solar Pump
- - Solar Chargers
- - Fiberglass Chopped Strand
- - Fiberglass Mesh Cloth
- - Composite Pipes
- - FRP Pultrusion Profiles
- - Fiberglass Mat Tissue
- - Fiberglass Fabrics
- - Fiberglass Mesh
- - Composite Tank
- - Fiberglass Mesh tape
- - Polymer
- - FRP Roofing Panel
- - Fiberglass Roving
- - Monolithic Refractories
- - Ceramic Fiber Products
- - Refractory Bricks
- - Raw Materials For Refractory
- - Suspended Platform
- - Cranes
- - Concrete Machinery
- - Earthmoving Machinery
- - Building Hoist
- - Road Building Machinery
- - Plastic Pipe Fittings
- - Plastic Tubes
- - Plastic Sheets
- - Agricultural Plastic Products
- - Plastic Nets
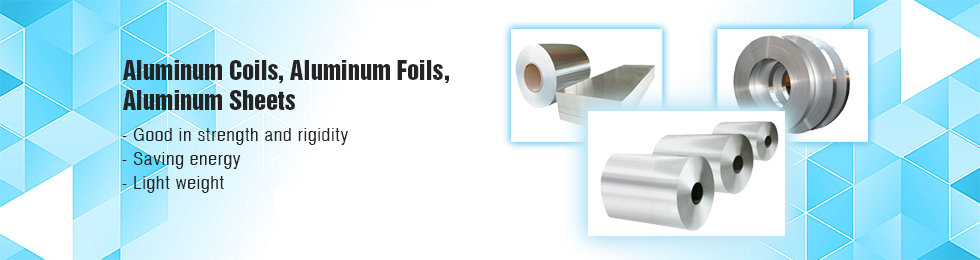
Q & A
How is the surface finish of aluminum coils prepared for painting or coating?
The surface finish of aluminum coils is typically prepared for painting or coating through a multi-step process. This process involves several stages, such as cleaning, etching, and chemical treatment. The purpose of cleaning is to remove any dirt, grease, or other contaminants from the surface. Etching is then performed to provide a microscopically roughened surface, which enhances adhesion of the paint or coating. Finally, a chemical treatment is applied to create a protective layer that improves corrosion resistance and promotes better paint adhesion. This prepared surface is then ready for painting or coating applications.
How are aluminum coils used in the production of heat exchangers for industrial applications?
Aluminum coils are commonly used in the production of heat exchangers for industrial applications due to their excellent thermal conductivity and corrosion resistance properties. These coils are typically formed into a serpentine shape and then placed within the heat exchanger unit. As hot fluid or gas flows through the coils, the aluminum material efficiently transfers the heat to the surrounding environment. This process facilitates effective heat exchange and allows for efficient cooling or heating in various industrial processes.
Can aluminum coils be employed in the production of ultra-high-speed trains?
Yes, aluminum coils can be employed in the production of ultra-high-speed trains. Aluminum is a lightweight and durable material that offers high strength-to-weight ratio, making it suitable for high-speed applications. Its use in coils allows for efficient electrical conductivity and heat dissipation, which are crucial in train systems. Additionally, aluminum's corrosion resistance properties contribute to the longevity and reliability of the trains.
How do you prevent corrosion in aluminum coils?
There are several ways to prevent corrosion in aluminum coils. One effective method is to apply a protective coating or finish, such as an epoxy or polyester coating, which creates a barrier between the coil and the environment. Regular cleaning and maintenance also play a crucial role in preventing corrosion, as any dirt or contaminants on the surface can accelerate the process. Additionally, ensuring proper ventilation and controlling humidity levels can help minimize the risk of corrosion by reducing moisture contact with the coils.
Wholesale Aluminum Coils from supplier in Zambia
We are a Aluminum Coils supplier serving the Zambia, mainly engaged in the sale, quotation, and technical support services of various Aluminum Coils products in the Zambia region. We are a subsidiary platform of the Fortune Global 500 company CNBM, able to provide you with one-stop Aluminum Coils procurement services in the Zambia. Not only do we have a wide range of Aluminum Coils products, but after years of market development in the Zambia, we can also provide valuable experience for your projects.