All Categories
- - Steel Wire Rod
- - Steel Coils
- - Steel Profiles
- - Steel Pipes
- - Stainless Steel
- - Tinplate
- - Special Steel
- - Steel Sheets
- - Steel Rebars
- - Steel Strips
- - Hot Rolled Steel
- - Cold Rolled Steel
- - Pre-painted Steel
- - Seamless Steel Pipe
- - Welded Steel Pipe
- - Hollow Steel Tubes
- - Galvanized Pipe
- - Stainless Steel Coil
- - Stainless Steel Sheet
- - Stainless Steel Plate
- - Stainless Steel Strips
- - Electrolytic Tinplate Coil
- - Electrolytic Tinplate Sheet
- - Stainless Steel Rebars
- - Solar Panels
- - Solar Water Heater
- - Solar Related Products
- - Solar Inverter
- - Solar Cells
- - Solar Light
- - Solar Energy Systems
- - Solar Controllers
- - Solar Mounting System
- - Solar Pump
- - Solar Chargers
- - Fiberglass Chopped Strand
- - Fiberglass Mesh Cloth
- - Composite Pipes
- - FRP Pultrusion Profiles
- - Fiberglass Mat Tissue
- - Fiberglass Fabrics
- - Fiberglass Mesh
- - Composite Tank
- - Fiberglass Mesh tape
- - Polymer
- - FRP Roofing Panel
- - Fiberglass Roving
- - Monolithic Refractories
- - Ceramic Fiber Products
- - Refractory Bricks
- - Raw Materials For Refractory
- - Suspended Platform
- - Cranes
- - Concrete Machinery
- - Earthmoving Machinery
- - Building Hoist
- - Road Building Machinery
- - Plastic Pipe Fittings
- - Plastic Tubes
- - Plastic Sheets
- - Agricultural Plastic Products
- - Plastic Nets
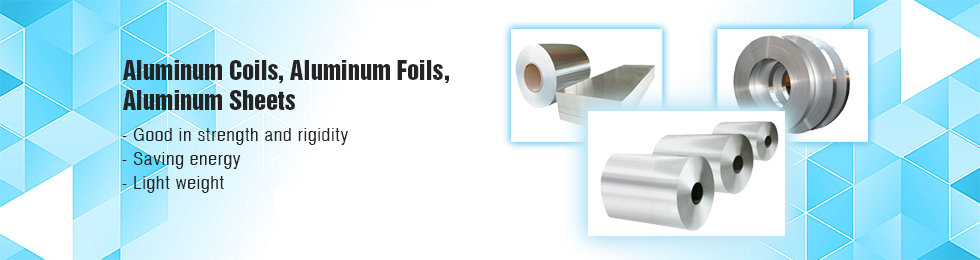
Q & A
What is the role of aluminum coils in the automotive industry's powertrain components?
Aluminum coils play a crucial role in the automotive industry's powertrain components as they are commonly used in the manufacturing of radiators and condensers. These coils are responsible for efficiently transferring heat away from the engine and other powertrain components, ensuring optimal performance and preventing overheating. Additionally, aluminum coils are lightweight, corrosion-resistant, and provide excellent thermal conductivity, making them an ideal choice for powertrain applications where weight reduction and heat dissipation are essential.
What is the impact of alloy composition on the properties of aluminum coils?
The alloy composition of aluminum coils significantly impacts their properties. By varying the composition, properties such as strength, corrosion resistance, and thermal conductivity can be tailored to specific requirements. For instance, adding elements like copper or magnesium can enhance the strength, while zinc can improve corrosion resistance. Additionally, altering alloy composition can also affect the coil's formability and weldability. Thus, understanding and controlling alloy composition is crucial in producing aluminum coils with desired properties for various applications.
What are the considerations for using aluminum coils in applications requiring high-temperature resistance?
When considering the use of aluminum coils in applications requiring high-temperature resistance, several factors should be taken into account. Firstly, aluminum has a relatively low melting point compared to other metals, so the temperature range needs to be within its limits. Secondly, aluminum's strength and structural integrity can be compromised at high temperatures, so the mechanical requirements of the application should be evaluated. Additionally, the presence of any corrosive elements or chemicals at high temperatures should be considered, as aluminum can be susceptible to corrosion in certain environments. Lastly, proper insulation and cooling mechanisms should be in place to prevent overheating and ensure efficient heat dissipation.
How are aluminum coils cut to specific lengths?
Aluminum coils are cut to specific lengths using a process called slitting. Slitting machines are used to unroll the coil, straighten it, and then pass it through rotating circular blades that cut the coil into narrower strips of the desired length. The slitting machine can be adjusted to achieve different widths and lengths, ensuring precise and accurate cuts.
Wholesale Aluminum Coils from supplier in Vanuatu
Whether you need Aluminum Coils for construction, manufacturing, or any other application, our team of experts can assist you in selecting the right product for your needs. We understand the importance of quality and reliability, which is why we only source our Aluminum Coils from trusted manufacturers.
In addition to our sales services, we also provide competitive quotations to ensure you receive the best value for your investment. Our pricing is transparent and fair, and we strive to offer the most cost-effective solutions without compromising on quality.
Furthermore, our technical support team is always available to answer any questions or concerns you may have. We have a deep understanding of the technical aspects of Aluminum Coils and can provide guidance on installation, maintenance, and troubleshooting.
At CNBM Vanuatu, customer satisfaction is our top priority. We are committed to delivering exceptional service and exceeding your expectations. Contact us today to discuss your Aluminum Coils requirements and experience the benefits of partnering with a leading supplier in Vanuatu.
In addition to our sales services, we also provide competitive quotations to ensure you receive the best value for your investment. Our pricing is transparent and fair, and we strive to offer the most cost-effective solutions without compromising on quality.
Furthermore, our technical support team is always available to answer any questions or concerns you may have. We have a deep understanding of the technical aspects of Aluminum Coils and can provide guidance on installation, maintenance, and troubleshooting.
At CNBM Vanuatu, customer satisfaction is our top priority. We are committed to delivering exceptional service and exceeding your expectations. Contact us today to discuss your Aluminum Coils requirements and experience the benefits of partnering with a leading supplier in Vanuatu.