All Categories
- - Steel Wire Rod
- - Steel Coils
- - Steel Profiles
- - Steel Pipes
- - Stainless Steel
- - Tinplate
- - Special Steel
- - Steel Sheets
- - Steel Rebars
- - Steel Strips
- - Hot Rolled Steel
- - Cold Rolled Steel
- - Pre-painted Steel
- - Seamless Steel Pipe
- - Welded Steel Pipe
- - Hollow Steel Tubes
- - Galvanized Pipe
- - Stainless Steel Coil
- - Stainless Steel Sheet
- - Stainless Steel Plate
- - Stainless Steel Strips
- - Electrolytic Tinplate Coil
- - Electrolytic Tinplate Sheet
- - Stainless Steel Rebars
- - Solar Panels
- - Solar Water Heater
- - Solar Related Products
- - Solar Inverter
- - Solar Cells
- - Solar Light
- - Solar Energy Systems
- - Solar Controllers
- - Solar Mounting System
- - Solar Pump
- - Solar Chargers
- - Fiberglass Chopped Strand
- - Fiberglass Mesh Cloth
- - Composite Pipes
- - FRP Pultrusion Profiles
- - Fiberglass Mat Tissue
- - Fiberglass Fabrics
- - Fiberglass Mesh
- - Composite Tank
- - Fiberglass Mesh tape
- - Polymer
- - FRP Roofing Panel
- - Fiberglass Roving
- - Monolithic Refractories
- - Ceramic Fiber Products
- - Refractory Bricks
- - Raw Materials For Refractory
- - Suspended Platform
- - Cranes
- - Concrete Machinery
- - Earthmoving Machinery
- - Building Hoist
- - Road Building Machinery
- - Plastic Pipe Fittings
- - Plastic Tubes
- - Plastic Sheets
- - Agricultural Plastic Products
- - Plastic Nets
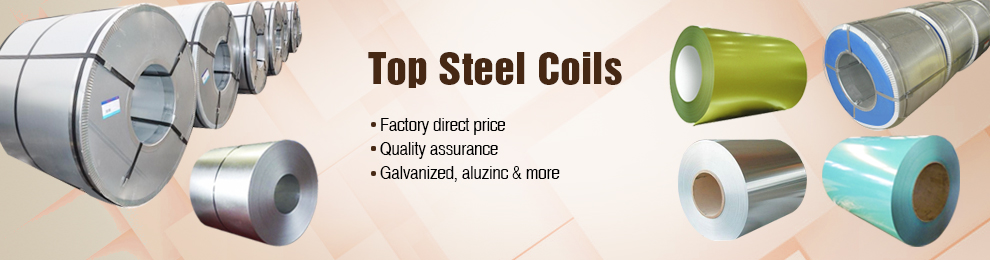
Q & A
How does tinplate compare to glass containers in terms of recycling?
Tinplate is generally considered more favorable than glass containers in terms of recycling. Tinplate is highly recyclable and can be reused multiple times without compromising its quality. It is also easier and more energy-efficient to recycle tinplate compared to glass containers, as the recycling process for tinplate requires less energy and produces fewer emissions. Additionally, the demand for recycled tinplate is high, making it a valuable material in the recycling industry. On the other hand, glass containers can also be recycled, but the process involves more energy consumption and requires sorting by color, which can be time-consuming and costly.
How is the thickness of tinplate coatings optimized for different industrial and consumer applications?
The thickness of tinplate coatings is optimized for different industrial and consumer applications through a combination of factors such as the desired level of corrosion resistance, the intended use and environment, cost considerations, and regulatory requirements. Extensive research, development, and testing are conducted to determine the ideal coating thickness that balances these factors. Additionally, feedback and collaboration with industry partners and customers play a crucial role in fine-tuning the coating thickness to meet specific application needs.
How does the weight of tinplate influence the overall efficiency of products?
The weight of tinplate can influence the overall efficiency of products in several ways. Firstly, a lighter weight tinplate can reduce transportation costs as it requires less fuel to transport. Secondly, it can enhance the ease of handling and maneuverability of products, leading to improved efficiency in production processes. Additionally, lighter tinplate can contribute to a reduction in overall packaging waste and environmental impact. However, it is important to maintain a balance between weight reduction and maintaining the necessary structural integrity and protection for the product.
How has the technology behind tinplate production evolved over the years?
The technology behind tinplate production has evolved significantly over the years. Initially, tinplate was produced using a manual process, where sheets of iron were dipped in molten tin to create a thin layer of tin coating. However, with advancements in technology, the process became more automated and efficient. Modern tinplate production involves continuous electroplating, where the sheets of iron are passed through an electrolyte bath, and an electric current is used to deposit a precise and uniform layer of tin on the surface. This automated process ensures higher quality and consistency in tinplate production, while also reducing costs and increasing productivity. Additionally, innovations in machinery and equipment have further improved the efficiency of tinplate production, allowing for faster production rates and improved overall performance. Overall, the technology behind tinplate production has undergone significant advancements, resulting in more efficient, cost-effective, and high-quality production methods.
Wholesale Tinplate from supplier in Belgium
We are a Tinplate supplier serving the Belgium, mainly engaged in the sale, quotation, and technical support services of various Tinplate products in the Belgium region. We are a subsidiary platform of the Fortune Global 500 company CNBM, able to provide you with one-stop Tinplate procurement services in the Belgium. Not only do we have a wide range of Tinplate products, but after years of market development in the Belgium, we can also provide valuable experience for your projects.