All Categories
- - Steel Wire Rod
- - Steel Coils
- - Steel Profiles
- - Steel Pipes
- - Stainless Steel
- - Tinplate
- - Special Steel
- - Steel Sheets
- - Steel Rebars
- - Steel Strips
- - Hot Rolled Steel
- - Cold Rolled Steel
- - Pre-painted Steel
- - Seamless Steel Pipe
- - Welded Steel Pipe
- - Hollow Steel Tubes
- - Galvanized Pipe
- - Stainless Steel Coil
- - Stainless Steel Sheet
- - Stainless Steel Plate
- - Stainless Steel Strips
- - Electrolytic Tinplate Coil
- - Electrolytic Tinplate Sheet
- - Stainless Steel Rebars
- - Solar Panels
- - Solar Water Heater
- - Solar Related Products
- - Solar Inverter
- - Solar Cells
- - Solar Light
- - Solar Energy Systems
- - Solar Controllers
- - Solar Mounting System
- - Solar Pump
- - Solar Chargers
- - Fiberglass Chopped Strand
- - Fiberglass Mesh Cloth
- - Composite Pipes
- - FRP Pultrusion Profiles
- - Fiberglass Mat Tissue
- - Fiberglass Fabrics
- - Fiberglass Mesh
- - Composite Tank
- - Fiberglass Mesh tape
- - Polymer
- - FRP Roofing Panel
- - Fiberglass Roving
- - Monolithic Refractories
- - Ceramic Fiber Products
- - Refractory Bricks
- - Raw Materials For Refractory
- - Suspended Platform
- - Cranes
- - Concrete Machinery
- - Earthmoving Machinery
- - Building Hoist
- - Road Building Machinery
- - Plastic Pipe Fittings
- - Plastic Tubes
- - Plastic Sheets
- - Agricultural Plastic Products
- - Plastic Nets
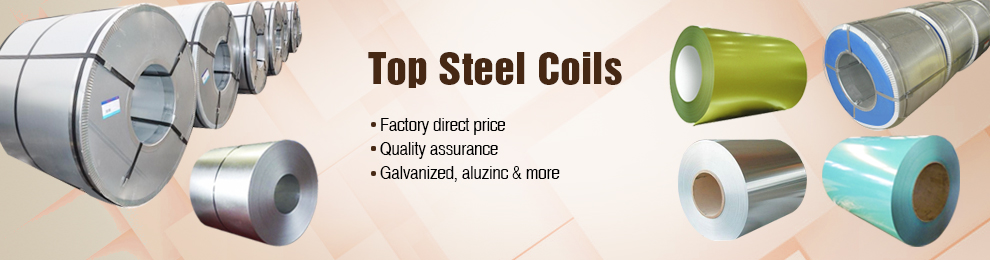
Q & A
Can welded steel pipes be used for chemical refineries?
Yes, welded steel pipes can be used for chemical refineries. Welded steel pipes are commonly used in various industries, including chemical refineries, due to their high strength, durability, and resistance to corrosion. They are suitable for transporting various chemicals and fluids, providing a reliable and efficient solution for the needs of chemical refineries.
What is the difference between butt welding and socket welding for welded steel pipe fittings?
Butt welding and socket welding are two different methods used for joining welded steel pipe fittings.
Butt welding involves the welding of two pipe fittings by aligning the ends of the pipes and then applying heat and pressure to create a strong and permanent bond. This method requires the use of a welding machine and skilled operators. Butt welding is commonly used for larger pipe fittings and in applications where a high level of strength and integrity is required.
Socket welding, on the other hand, involves the insertion of one pipe fitting into the socket of another fitting and then welding the joint. This method does not require the use of a welding machine and is often used for smaller pipe fittings and in applications where a tight seal is desired. Socket welding is relatively easier to perform compared to butt welding but may not offer the same level of strength as butt welding.
In summary, the main differences between butt welding and socket welding for welded steel pipe fittings lie in the joining method and the level of strength and integrity achieved. Butt welding is typically used for larger fittings and offers a higher level of strength, while socket welding is commonly used for smaller fittings and provides a tighter seal.
How long do welded steel pipes typically last?
Welded steel pipes typically have a long lifespan and can last for several decades, depending on various factors such as the quality of the steel, the conditions in which they are used, and the level of maintenance they receive.
How is a welded steel pipe different from a seamless steel pipe?
A welded steel pipe is created by joining two or more steel plates or coils through a welding process, whereas a seamless steel pipe is formed from a solid cylindrical steel billet without any seams. The main difference lies in their manufacturing methods, with the welded pipe being more cost-effective and suitable for applications with lower pressure and temperature requirements, while the seamless pipe offers higher strength, durability, and is preferred for high-pressure and high-temperature applications.
What are the common defects found in welded steel pipe?
Some common defects found in welded steel pipes include lack of fusion, porosity, cracks, undercutting, and misalignment. Lack of fusion occurs when the weld metal does not properly fuse with the base metal, leading to weak joints. Porosity refers to the presence of air pockets or voids in the weld, which can weaken the structure. Cracks can develop due to excessive heat or stress during welding, compromising the integrity of the pipe. Undercutting occurs when the base metal is eroded along the edges of the weld, resulting in a groove that weakens the joint. Misalignment refers to a deviation from the desired position of the weld, leading to improper fusion and potential structural issues.
Wholesale Welded Steel Pipe from supplier in Nepal
We are a Welded Steel Pipe supplier serving the Nepal, mainly engaged in the sale, quotation, and technical support services of various Welded Steel Pipe products in the Nepal region. We are a subsidiary platform of the Fortune Global 500 company CNBM, able to provide you with one-stop Welded Steel Pipe procurement services in the Nepal. Not only do we have a wide range of Welded Steel Pipe products, but after years of market development in the Nepal, we can also provide valuable experience for your projects.