All Categories
- - Steel Wire Rod
- - Steel Coils
- - Steel Profiles
- - Steel Pipes
- - Stainless Steel
- - Tinplate
- - Special Steel
- - Steel Sheets
- - Steel Rebars
- - Steel Strips
- - Hot Rolled Steel
- - Cold Rolled Steel
- - Pre-painted Steel
- - Seamless Steel Pipe
- - Welded Steel Pipe
- - Hollow Steel Tubes
- - Galvanized Pipe
- - Stainless Steel Coil
- - Stainless Steel Sheet
- - Stainless Steel Plate
- - Stainless Steel Strips
- - Electrolytic Tinplate Coil
- - Electrolytic Tinplate Sheet
- - Stainless Steel Rebars
- - Solar Panels
- - Solar Water Heater
- - Solar Related Products
- - Solar Inverter
- - Solar Cells
- - Solar Light
- - Solar Energy Systems
- - Solar Controllers
- - Solar Mounting System
- - Solar Pump
- - Solar Chargers
- - Fiberglass Chopped Strand
- - Fiberglass Mesh Cloth
- - Composite Pipes
- - FRP Pultrusion Profiles
- - Fiberglass Mat Tissue
- - Fiberglass Fabrics
- - Fiberglass Mesh
- - Composite Tank
- - Fiberglass Mesh tape
- - Polymer
- - FRP Roofing Panel
- - Fiberglass Roving
- - Monolithic Refractories
- - Ceramic Fiber Products
- - Refractory Bricks
- - Raw Materials For Refractory
- - Suspended Platform
- - Cranes
- - Concrete Machinery
- - Earthmoving Machinery
- - Building Hoist
- - Road Building Machinery
- - Plastic Pipe Fittings
- - Plastic Tubes
- - Plastic Sheets
- - Agricultural Plastic Products
- - Plastic Nets
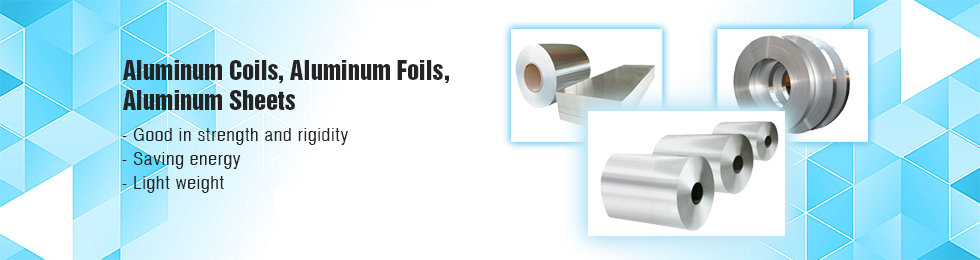
Q & A
How can aluminum profiles be adapted for high-temperature applications, such as in industrial furnaces?
Aluminum profiles can be adapted for high-temperature applications in industrial furnaces by utilizing specific alloys that are designed to withstand elevated temperatures. These alloys, such as aluminum 6061, 6063, or 7075, possess increased thermal stability and strength, making them suitable for such environments. Additionally, the profiles can be treated with various surface coatings or finishes to enhance their heat resistance and protect them from oxidation or corrosion. Proper design considerations, such as incorporating thermal barriers or insulation, can also help in minimizing heat transfer and ensuring the profiles perform optimally in high-temperature settings.
What surface finishes are commonly used to enhance the appearance and protection of aluminum profiles?
Some commonly used surface finishes to enhance the appearance and protection of aluminum profiles include anodizing, powder coating, and polishing.
What is the process of powder coating aluminum profiles?
The process of powder coating aluminum profiles involves several steps. First, the aluminum profiles are thoroughly cleaned to remove any dirt, grease, or other contaminants. This is typically done using a combination of chemical cleaners and water.
Once the profiles are clean, they are pre-treated with a chemical solution to improve adhesion and corrosion resistance. This step, known as pre-treatment or etching, helps the powder coating adhere to the aluminum surface.
After pre-treatment, the aluminum profiles are dried to ensure there is no moisture left on the surface. This is important for achieving a smooth and even coating.
Next, the powder coating material is applied to the aluminum profiles. This is done using a spray gun or an electrostatic process. The powder is attracted to the electrically grounded aluminum profiles, ensuring even coverage.
Once the powder is applied, the aluminum profiles are moved into an oven for curing. The heat in the oven causes the powder to melt and flow, forming a hard and durable coating. The profiles are typically heated at a specific temperature for a specific amount of time to achieve the desired coating properties.
After curing, the aluminum profiles are cooled down and inspected for any defects or imperfections. If necessary, they may undergo additional processes such as sanding or polishing to improve the surface finish.
Overall, the process of powder coating aluminum profiles involves cleaning, pre-treatment, powder application, curing, cooling, and final inspection to achieve a high-quality and long-lasting coating.
Wholesale Aluminum Profiles from supplier in Czech Republic
Our team of experts is committed to providing excellent customer service and delivering high-quality Aluminum Profiles products that meet international standards. We work closely with our customers to understand their requirements and provide customized solutions that suit their individual needs.
Whether you are in the construction, automotive, or manufacturing industry, our Aluminum Profiles products can be used in a variety of applications. From windows and doors to curtain walls and industrial machinery, our profiles offer durability, strength, and aesthetic appeal.
At our company, we prioritize sustainability and environmental responsibility. Our Aluminum Profiles are made from recycled materials and are fully recyclable, making them an eco-friendly choice. We also ensure that our manufacturing processes adhere to strict environmental standards.
When you choose us as your supplier of Aluminum Profiles in the Czech Republic, you can expect reliable and timely delivery, competitive pricing, and exceptional customer service. We are dedicated to building long-term partnerships with our customers and helping them achieve their goals.
Contact us today to discuss your Aluminum Profiles requirements and let us provide you with a tailored solution that meets your needs in the Czech Republic market.
Whether you are in the construction, automotive, or manufacturing industry, our Aluminum Profiles products can be used in a variety of applications. From windows and doors to curtain walls and industrial machinery, our profiles offer durability, strength, and aesthetic appeal.
At our company, we prioritize sustainability and environmental responsibility. Our Aluminum Profiles are made from recycled materials and are fully recyclable, making them an eco-friendly choice. We also ensure that our manufacturing processes adhere to strict environmental standards.
When you choose us as your supplier of Aluminum Profiles in the Czech Republic, you can expect reliable and timely delivery, competitive pricing, and exceptional customer service. We are dedicated to building long-term partnerships with our customers and helping them achieve their goals.
Contact us today to discuss your Aluminum Profiles requirements and let us provide you with a tailored solution that meets your needs in the Czech Republic market.