All Categories
- - Steel Wire Rod
- - Steel Coils
- - Steel Profiles
- - Steel Pipes
- - Stainless Steel
- - Tinplate
- - Special Steel
- - Steel Sheets
- - Steel Rebars
- - Steel Strips
- - Hot Rolled Steel
- - Cold Rolled Steel
- - Pre-painted Steel
- - Seamless Steel Pipe
- - Welded Steel Pipe
- - Hollow Steel Tubes
- - Galvanized Pipe
- - Stainless Steel Coil
- - Stainless Steel Sheet
- - Stainless Steel Plate
- - Stainless Steel Strips
- - Electrolytic Tinplate Coil
- - Electrolytic Tinplate Sheet
- - Stainless Steel Rebars
- - Solar Panels
- - Solar Water Heater
- - Solar Related Products
- - Solar Inverter
- - Solar Cells
- - Solar Light
- - Solar Energy Systems
- - Solar Controllers
- - Solar Mounting System
- - Solar Pump
- - Solar Chargers
- - Fiberglass Chopped Strand
- - Fiberglass Mesh Cloth
- - Composite Pipes
- - FRP Pultrusion Profiles
- - Fiberglass Mat Tissue
- - Fiberglass Fabrics
- - Fiberglass Mesh
- - Composite Tank
- - Fiberglass Mesh tape
- - Polymer
- - FRP Roofing Panel
- - Fiberglass Roving
- - Monolithic Refractories
- - Ceramic Fiber Products
- - Refractory Bricks
- - Raw Materials For Refractory
- - Suspended Platform
- - Cranes
- - Concrete Machinery
- - Earthmoving Machinery
- - Building Hoist
- - Road Building Machinery
- - Plastic Pipe Fittings
- - Plastic Tubes
- - Plastic Sheets
- - Agricultural Plastic Products
- - Plastic Nets
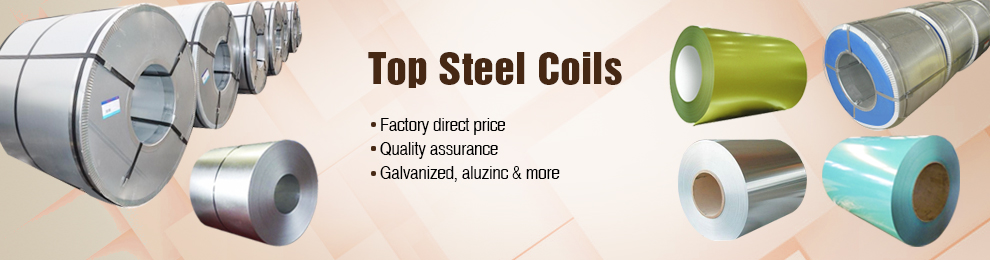
Q & A
What are the main factors that affect the corrosion resistance of electrolytic tinplate coil in food and beverage environments?
The main factors that affect the corrosion resistance of electrolytic tinplate coil in food and beverage environments include the acidity or pH level of the food or beverage, the presence of chloride ions, temperature, and the duration of exposure.
What are the factors affecting the price of electrolytic tinplate coil?
The factors affecting the price of electrolytic tinplate coil include the cost of raw materials such as tin, steel, and other alloying elements, the demand and supply dynamics in the market, production and manufacturing costs, transportation and logistics expenses, exchange rates, government policies and regulations, and overall economic conditions. Factors such as changes in tin prices, fluctuations in steel prices, variations in demand from industries such as packaging, automotive, and construction sectors, and geopolitical events can also impact the price of electrolytic tinplate coil.
How is the surface roughness measured on electrolytic tinplate coil?
The surface roughness on electrolytic tinplate coil is typically measured using a profilometer or a surface roughness tester. These instruments scan the surface of the tinplate coil and measure the variations in height to determine the roughness. The results are often expressed in terms of roughness parameters such as Ra (average roughness) or Rz (average maximum height).
What are the typical lead times for electrolytic tinplate coil orders?
The typical lead times for electrolytic tinplate coil orders can vary depending on factors such as quantity, supplier availability, and production schedules. However, on average, lead times for such orders can range between a few weeks to a couple of months. It is advisable to confirm specific lead times with the supplier or manufacturer when placing an order.
What are the common methods for cutting and shaping electrolytic tinplate coil?
The common methods for cutting and shaping electrolytic tinplate coil include shearing, slitting, blanking, and forming. Shearing involves using a sharp blade or scissors to cut the coil into desired shapes. Slitting involves cutting the coil into narrower strips using rotating circular blades. Blanking is a process where a punch and die are used to cut out specific shapes from the coil. Forming involves bending or shaping the tinplate coil using various tools and equipment.
Wholesale Electrolytic Tinplate Coil from supplier in Denmark
Our team of experts is dedicated to providing excellent customer service and ensuring that our customers in Denmark receive high-quality Electrolytic Tinplate Coils that meet their specific requirements. We understand the importance of timely delivery and competitive pricing, and we strive to meet and exceed our customers' expectations in these areas.
In addition to our sales and procurement services, we also offer technical support to assist our customers with any questions or concerns they may have regarding our Electrolytic Tinplate Coil products. Our knowledgeable team can provide guidance on product specifications, application recommendations, and troubleshooting, ensuring that our customers have a seamless experience from start to finish.
As a subsidiary of CNBM, a Fortune Global 500 company, we have the resources and network to source a wide range of Electrolytic Tinplate Coil products from reputable manufacturers. We have established strong relationships with suppliers, allowing us to offer competitive pricing and a diverse selection of products to our customers in Denmark.
Over the years, we have gained valuable experience in the Danish market and have developed a deep understanding of the unique needs and preferences of our customers. This enables us to provide valuable insights and recommendations for your projects, helping you make informed decisions and achieve successful outcomes.
Whether you are looking for Electrolytic Tinplate Coils for packaging applications, can making, or other industrial uses, we are confident in our ability to meet your needs. Contact us today to discuss your requirements and let us assist you in finding the perfect Electrolytic Tinplate Coil solution for your business in Denmark.
In addition to our sales and procurement services, we also offer technical support to assist our customers with any questions or concerns they may have regarding our Electrolytic Tinplate Coil products. Our knowledgeable team can provide guidance on product specifications, application recommendations, and troubleshooting, ensuring that our customers have a seamless experience from start to finish.
As a subsidiary of CNBM, a Fortune Global 500 company, we have the resources and network to source a wide range of Electrolytic Tinplate Coil products from reputable manufacturers. We have established strong relationships with suppliers, allowing us to offer competitive pricing and a diverse selection of products to our customers in Denmark.
Over the years, we have gained valuable experience in the Danish market and have developed a deep understanding of the unique needs and preferences of our customers. This enables us to provide valuable insights and recommendations for your projects, helping you make informed decisions and achieve successful outcomes.
Whether you are looking for Electrolytic Tinplate Coils for packaging applications, can making, or other industrial uses, we are confident in our ability to meet your needs. Contact us today to discuss your requirements and let us assist you in finding the perfect Electrolytic Tinplate Coil solution for your business in Denmark.